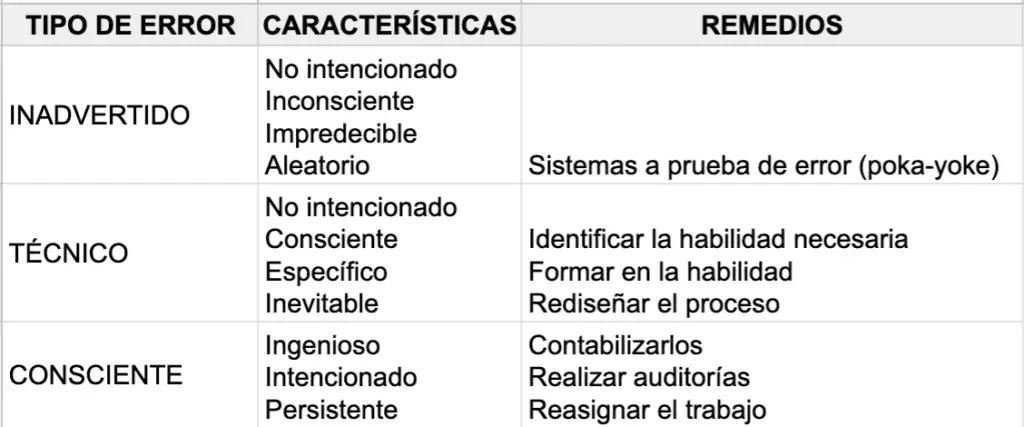
Niveles de poka yoke
Poka-yoke ppt
El Poka-yoke es una herramienta de fabricación ajustada que se refiere a la “prueba de errores” de un proceso. Fue acuñado originalmente por Shigeo Shingo en la década de 1960 y aplicado en Toyota como parte del Sistema de Producción Toyota (TPS).
El Poka-yoke también está presente en nuestra vida cotidiana, aunque muchos ejemplos son tan mundanos que a menudo no nos damos cuenta de que están ahí. La prevención de errores en la vida cotidiana va desde los dispositivos de seguridad que evitan que nos lesionemos hasta el corrector ortográfico, que simplemente evita que cometamos errores de ortografía que nos hagan parecer tontos.
Los coches están equipados con muchas funciones “a prueba de errores” para mantenernos seguros en la carretera. Muchos coches emiten un pitido o se iluminan si las puertas están abiertas con el motor en marcha, o si alguien está en el asiento del copiloto y no lleva abrochado el cinturón de seguridad. Estos son ejemplos de funciones de advertencia, que alertan a los usuarios de posibles errores.
La tecnología de seguridad ha avanzado mucho en los últimos años. Hoy en día, muchos coches vienen equipados con sensores que alertan a los conductores si se salen de su carril o les avisan si están demasiado cerca de otro coche (u otro objeto).
3 tipos de poka-yoke pdf
La competencia en los negocios aumenta constantemente. Ahora más que nunca, ofrecer productos y servicios de alta calidad es la clave para sobrevivir y crecer en el mercado actual. Ya sea en la industria manufacturera, la sanidad o los servicios, las empresas se esfuerzan por conseguir cero defectos. Aunque cero defectos suena muy bien, parece casi imposible de conseguir. El hecho es que los errores ocurren y los errores pueden ocurrir en todo tipo de procesos. Un operario de una máquina o un oficinista puede distraerse u olvidarse de completar una tarea, o una máquina puede romper una herramienta y provocar un error. Muchas empresas confían en la formación y las instrucciones de trabajo para evitar los errores. La información histórica indica que, independientemente de la formación que reciba el operario o de lo bien documentado que esté el proceso, se producen errores humanos. Aunque la aplicación de prácticas de trabajo estándar y la formación de los operarios son métodos válidos para reducir la frecuencia de los errores, no evitarán que éstos se produzcan. Las metodologías Mistake Proofing o Poka-Yoke pueden detectar los errores y evitar que la pieza no conforme pase al siguiente proceso o salga de sus instalaciones. Además, al aplicar técnicas de Error Proofing para detectar el error en su origen, podemos evitar que se produzca la pieza o el producto no conforme. Entonces estaremos realmente en el camino hacia los cero defectos.
Ejemplos de poka-yoke
A Shigeo Shingo se le atribuye este concepto que implica algún tipo de mecanismo que ayuda a evitar (yokeru) los errores (poka). Poka-yoke es el término japonés que corresponde a la prueba de errores. El Mistake Proofing consiste en añadir técnicas para prevenir los defectos y detectarlos tan pronto como
Intentar reducir la gravedad del error y del defecto.Objetivo:PREVENIR que se produzca un defecto y, cuando esto no sea posible, DETECTAR el defecto cada vez que se produzca. Existen varios niveles, esfuerzos y costes de la comprobación de errores. El equipo debe identificar los estados óptimos y examinar la viabilidad de su aplicación en los nuevos productos o procesos KPIV. El objetivo es en esta prioridad:1.Prevenir los errores que conducen a
Shigeo Shingo acuñó tres tipos de poka-yokes: Los defectos encontrados en operaciones o pasos posteriores de un proceso tienen más costes asociados. Hay más materiales, mano de obra, gastos generales, producto previamente reelaborado que están en riesgo. En última instancia, si el producto llega al cliente con un defecto, los intangibles, como la reputación, pueden superar el coste tangible.Por ejemplo, un detector de monóxido de carbono no será tan eficaz si no se conocen las entradas de los niveles peligrosos y tolerables de PPM, o si no está claro el lugar adecuado para su instalación.BUENO: Detecta el defecto antes de pasar al siguiente paso.MEJOR: Detecta los defectos durante el proceso en una operación.MEJOR: Evita que los defectos se produzcan en absoluto.Cada proceso debe contar con una prueba de errores para garantizar que los defectos no pasen al siguiente paso y que cada operación cuente con una prueba de errores para garantizar que sólo se acepten piezas sin defectos.
Niveles a prueba de errores
Muchas cosas pueden salir mal en el complejo entorno del lugar de trabajo. Todos los días hay oportunidades de cometer errores que darán lugar a productos defectuosos. Detrás del Poka Yoke (prueba de errores) está la convicción de que no es aceptable producir ni un solo producto defectuoso. Para convertirse en un competidor de talla mundial, una organización debe adoptar la filosofía y las prácticas de producir cero defectos. En este contexto, Deming expresó apropiadamente: “El problema es su proceso y no las personas; el 85% de las razones del fracaso son deficiencias en los sistemas y procesos más que en el empleado. El papel de la dirección es cambiar el proceso en lugar de presionar a los individuos para que lo hagan mejor”. Los métodos a prueba de errores son uno de los medios probados para lograr este objetivo. Shigeo Shingo, fundador de Poka Yoke, se dio cuenta de las limitaciones de las técnicas estadísticas e ideó un proceso de tres pasos de ZQC (Zero Quality Control). Basado en la profunda sabiduría de los proverbios, como “Errar es humano” y “Más vale prevenir que curar”, Poka Yoke es un enfoque basado en la técnica para lograr el ZDQ (Zero Defect Quality). Este enfoque de sentido común, que se basa principalmente en la vigilancia de las máquinas en lugar de la vigilancia humana, permitió a Toyota ser tan rentable.